9 Indicadores de manutenção industrial para acompanhar
A gestão de manutenção é uma das áreas essenciais para a eficiência e continuidade das operações fabris. Para monitorar e otimizar o desempenho dos ativos, é fundamental acompanhar indicadores de manutenção industrial, já que eles oferecem informações sobre a confiabilidade dos equipamentos e a performance dos processos.
O entendimento e o uso dessas métricas podem reduzir custos, melhorar a produtividade e garantir prazos mais confiáveis para a indústria. MTBF (Mean Time Between Failures) e MTTR (Mean Time To Repair), por exemplo, ajudam a saber o tempo de falha e o tempo necessário para reparos.
Neste conteúdo, você conhecerá os 9 principais indicadores de manutenção industrial, sua importância, além de como, calculá-los e utilizá-los para otimizar os resultados da sua operação. Acompanhe!
O que são indicadores de manutenção industrial?
Indicadores de manutenção industrial são métricas utilizadas para medir e avaliar a eficiência da manutenção de equipamentos e ativos na produção. Eles ajudam a identificar pontos críticos de falha, otimizar recursos e garantir a continuidade da operação.
Entender e usar os indicadores é muito importante para indústrias que buscam melhorar sua performance. Afinal, eles possibilitam a identificação de problemas e a adoção de medidas corretivas antes que eles se tornem falhas críticas.
Quais são os principais indicadores de manutenção industrial?
Após entender o conceito, vamos detalhar os principais indicadores de manutenção industrial. Confira!
1. MTBF (Mean Time Between Failures)
O MTBF é uma das métricas mais importantes e representa o tempo médio entre falhas de um sistema ou equipamento. Ele é usado para medir a confiabilidade de uma máquina. Assim, quanto maior o MTBF, mais confiável é o equipamento.
Falhas frequentes indicam que o equipamento precisa de mais atenção e talvez seja hora de revisar os processos de manutenção. Portanto, monitorar o indicador é essencial para prever a necessidade de manutenção preventiva, minimizar paradas inesperadas e otimizar a produtividade.
Como calcular o MTBF
A fórmula básica para encontrar o MTBF é (TD – TM) ÷ P, onde:
- TD: tempo real de disponibilidade;
- TM: tempo total de manutenção;
- P: quantidade de paradas.
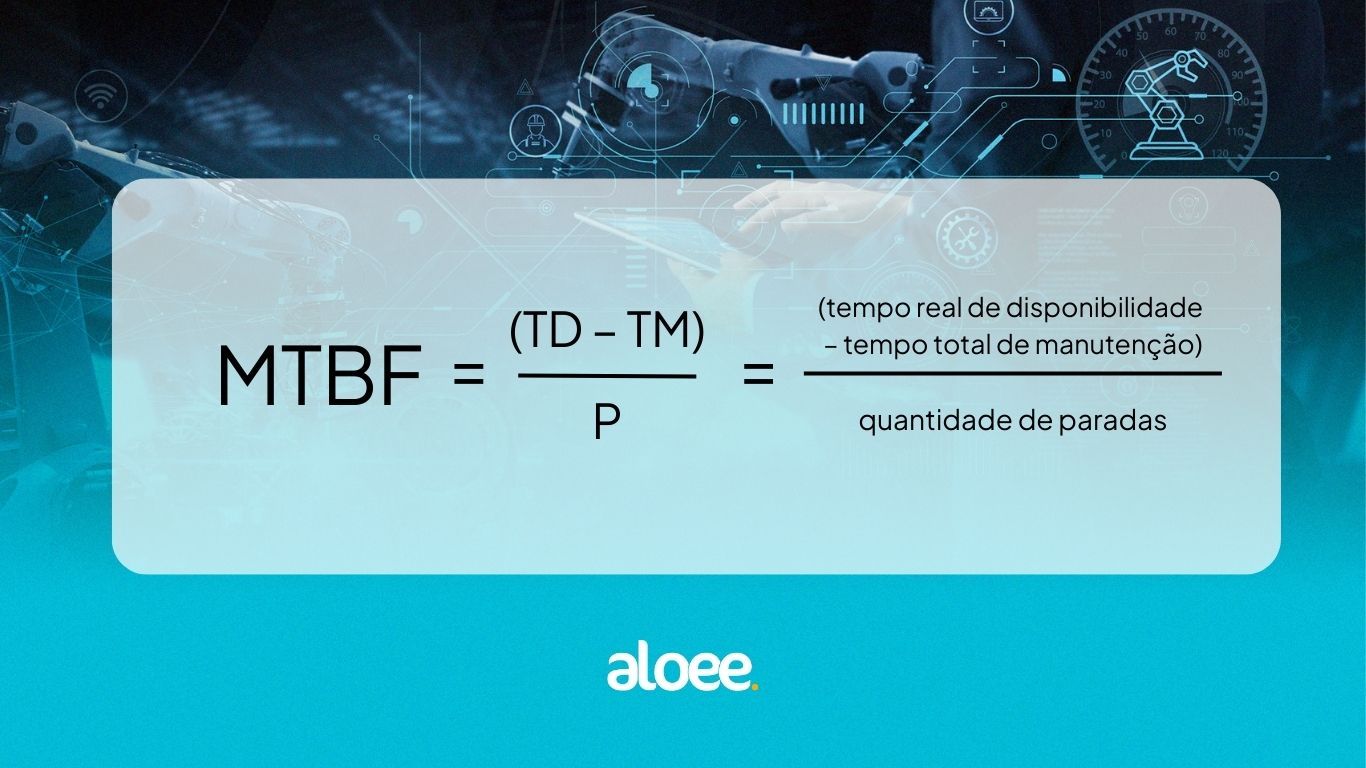
Exemplo: se uma máquina ficou disponível por 1.000 horas (TD) e, nesse período, passou 100 horas em manutenção (TM), com 10 paradas (P), temos o seguinte: MTBF é: (1000 – 100) ÷ 10 = 900 ÷ 10 = 90 horas. Isso significa que o tempo médio entre falhas dessa máquina é de 90 horas. Ou seja, a cada 90 horas de operação, em média, ocorre uma nova falha.
2. MTTR (Mean Time To Repair)
O MTTR mede o tempo médio necessário para reparar uma falha e retornar a máquina ao seu funcionamento normal. Essa métrica é importante para avaliar a eficiência das equipes de manutenção e o tempo de resposta das reparações.
Reduzir o MTTR, um dos principais indicadores de manutenção industrial, significa minimizar o impacto das falhas no processo produtivo. Quanto menor esse tempo médio de reparo, maior a capacidade da equipe em restaurar os ativos rapidamente — o que garante mais tempo de produção e menos interrupções nas operações.
Como calcular o MTTR
A fórmula básica para o MTTR é tempo total de manutenção ÷ número de paradas.
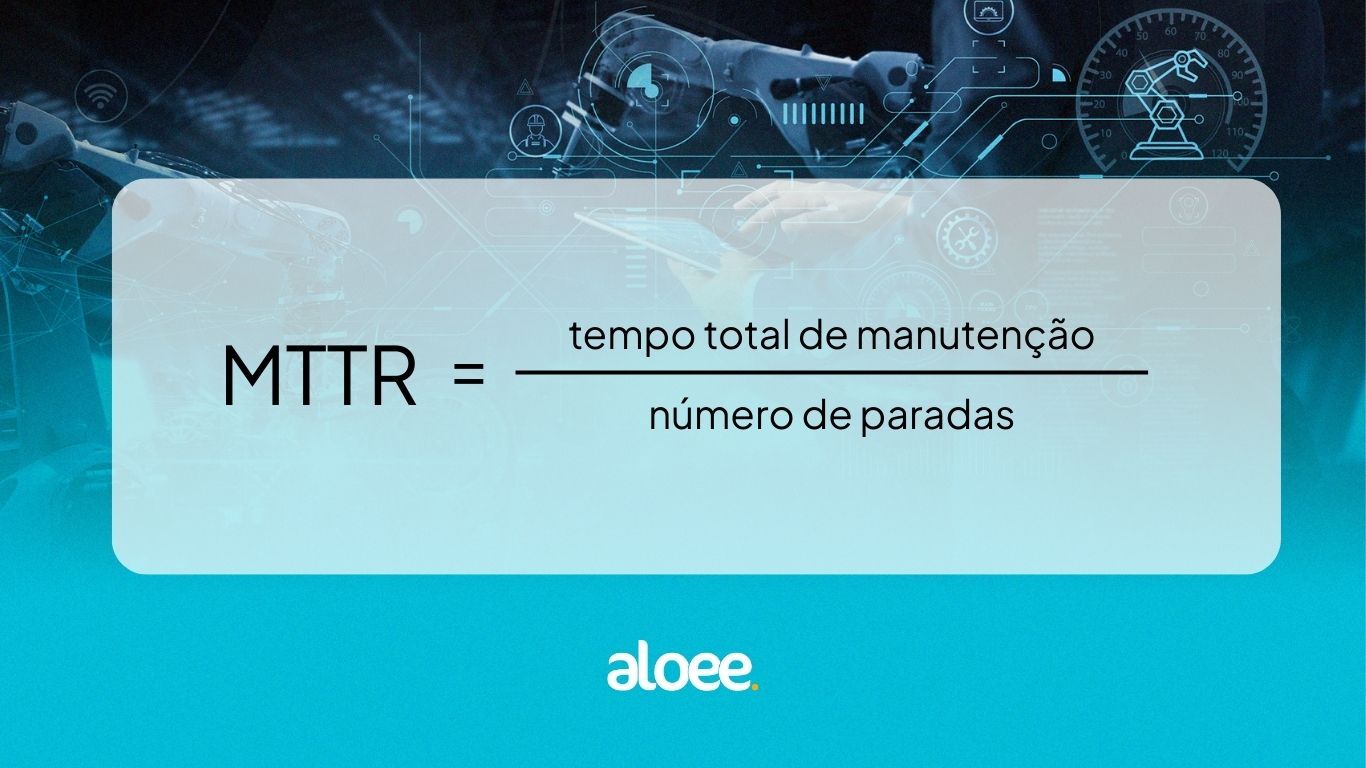
Exemplo: imagine que um equipamento apresentou 5 falhas ao longo de um mês e que, somando todos os atendimentos, foram gastas 20 horas em manutenção. Com a fórmula, chegamos a este cálculo: 20 ÷ 5 = 4. Em média, são necessárias 4 horas para reparar a máquina a cada falha registrada.
3. Disponibilidade
A Disponibilidade refere-se ao tempo total em que um equipamento está disponível para produção. Isto é, trata-se da porcentagem de tempo em que ele está em operação comparado ao tempo total.
Uma baixa disponibilidade geralmente indica problemas recorrentes de falhas ou manutenção ineficaz, por exemplo. Dessa forma, entender e acompanhar o indicador é importante para medir a eficácia da manutenção e determinar se os ativos estão operando no máximo de sua capacidade.
Como calcular a Disponibilidade
O cálculo é: Disponibilidade = (Tempo de operação ÷ Tempo total planejado) × 100
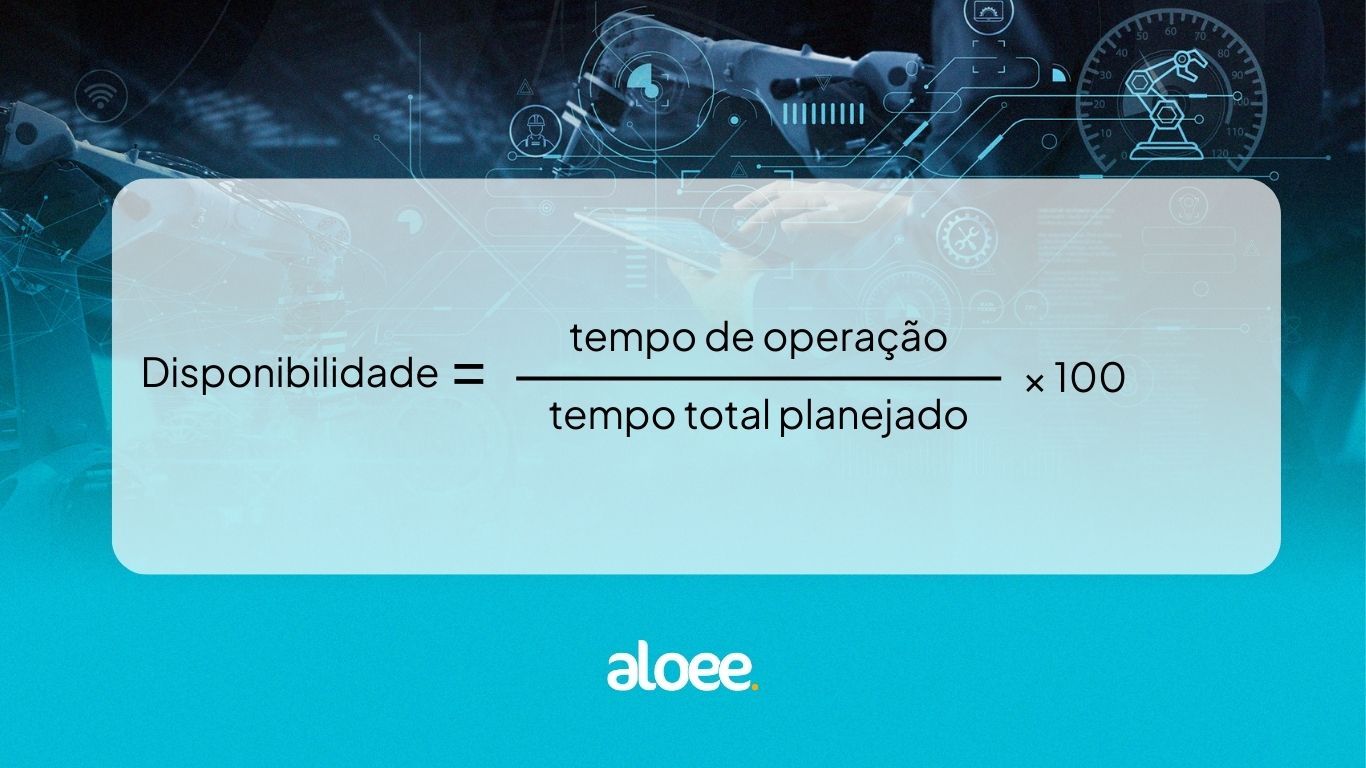
Exemplo: suponha que uma máquina tenha sido programada para funcionar por 200 horas em um mês, mas ficou em operação apenas 170 horas devido a falhas e manutenções. Veja a aplicação da fórmula: (170 ÷ 200) × 100 = 85%. Isso significa que a máquina esteve disponível para produção em 85% do tempo planejado.
4. Backlog
O Backlog de manutenção, por sua vez, é a quantidade de manutenção pendente — ou seja, o número de ordens de serviço que ainda não foram realizadas. A métrica é usada para avaliar a sobrecarga da equipe e identificar possíveis falhas na gestão de manutenção preventiva.
O monitoramento de indicadores de manutenção industrial como esse permite evitar o acúmulo de tarefas — situação que pode gerar falhas inesperadas e elevar os custos operacionais. Com o controle adequado do backlog, é possível priorizar tarefas críticas e garantir uma manutenção mais eficiente.
Como calcular o Backlog
Para chegar ao número, faça este cálculo:
Backlog (em semanas) = Total de horas de manutenção pendentes ÷ Capacidade semanal da equipe de manutenção (em horas)
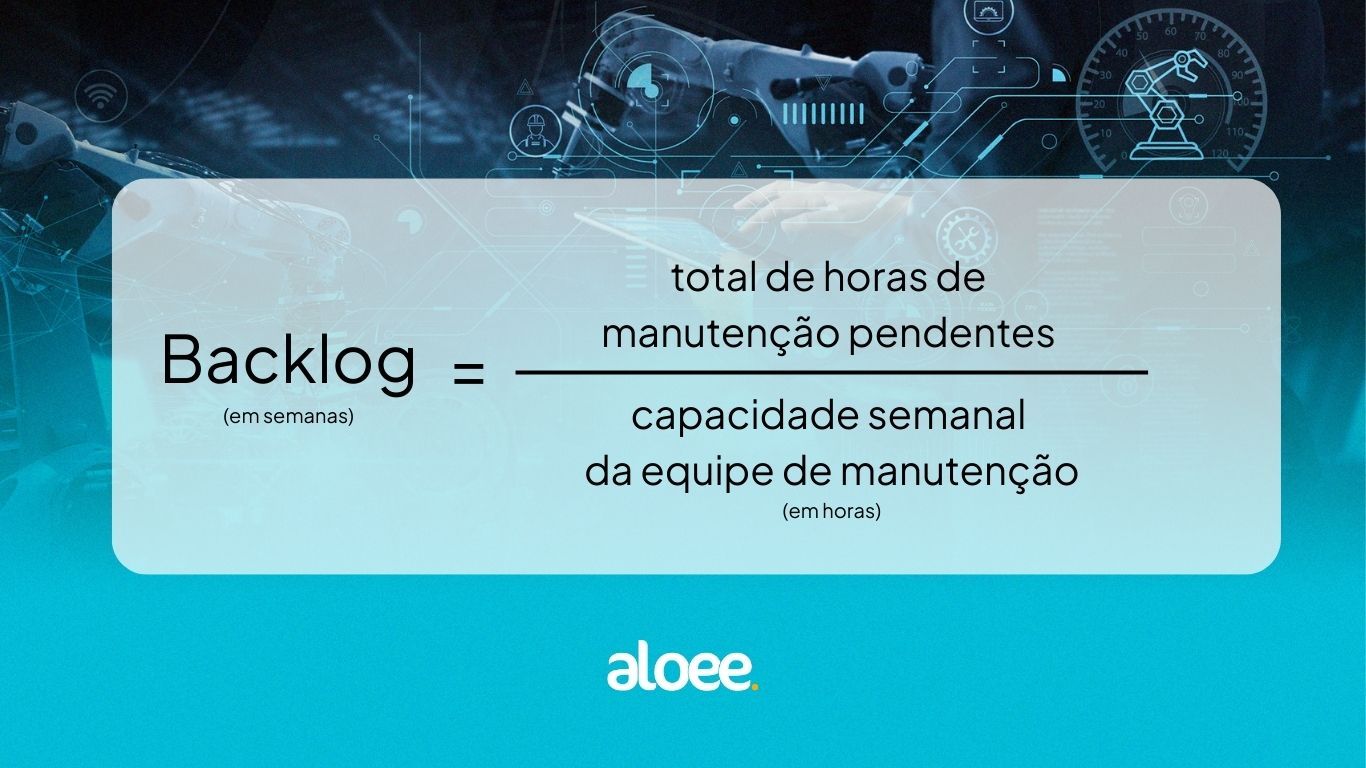
Exemplo: caso o seu time de manutenção tenha uma capacidade de 160 horas semanais (4 técnicos × 40 horas) e existem 480 horas de ordens de serviço pendentes, o cálculo seria: Backlog = 480 ÷ 160 = 3 semanas. Na prática, seriam necessárias 3 semanas para zerar as tarefas acumuladas, sem receber novas ordens nesse período.
5. Confiabilidade
Como o nome sugere, a Confiabilidade de um ativo é a sua capacidade de realizar funções sem falhas por um período determinado. Ela está diretamente relacionada ao MTBF, mas também envolve o desempenho consistente ao longo do tempo.
Essa métrica é fundamental para observar se os equipamentos cumprem suas funções de forma contínua e eficaz, minimizando os riscos de paradas inesperadas.
Como calcular a Confiabilidade
A fórmula desse indicador de manutenção industrial é: Confiabilidade (R) = e^(-t ÷ MTBF), em que:
- R: Confiabilidade (probabilidade de não falhar)
- e: constante matemática (~2,718)
- t: tempo de operação desejado
- MTBF: tempo médio entre falhas
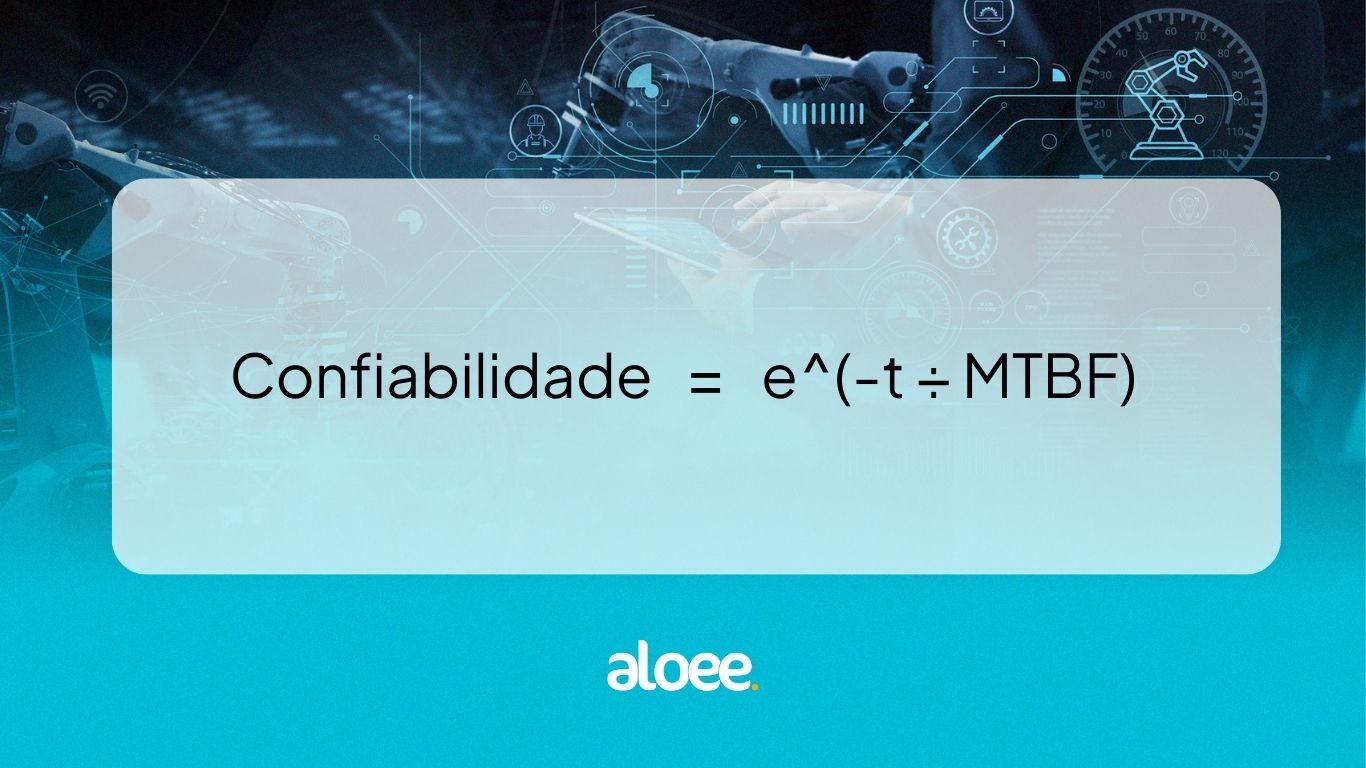
Exemplo: caso o MTBF de uma máquina seja de 100 horas, e você quiser saber a probabilidade de ela operar por 50 horas sem falhas, calcule desta forma: R = e^(-50 / 100) ≈ e^(-0,5) ≈ 0,6065. Em outras palavras, a Confiabilidade nesse período é de aproximadamente 60,65%.
6. CMF (Custo de Manutenção sobre Faturamento)
O CMF é um indicador relacionado a finanças que compara o custo de manutenção com o faturamento da empresa. Ele é útil para entender o impacto financeiro dessas atividades no orçamento da empresa.
A métrica ajuda a controlar os gastos e a assegurar que a manutenção seja realizada de forma eficiente, sem comprometer o caixa. Ao manter o CMF sob controle, é possível evitar desembolsos excessivos, ao mesmo tempo em que mantém os ativos em boas condições.
Como calcular o CMF
A fórmula para o CMF é
(Custo Total de Manutenção ÷ Faturamento Total) × 100
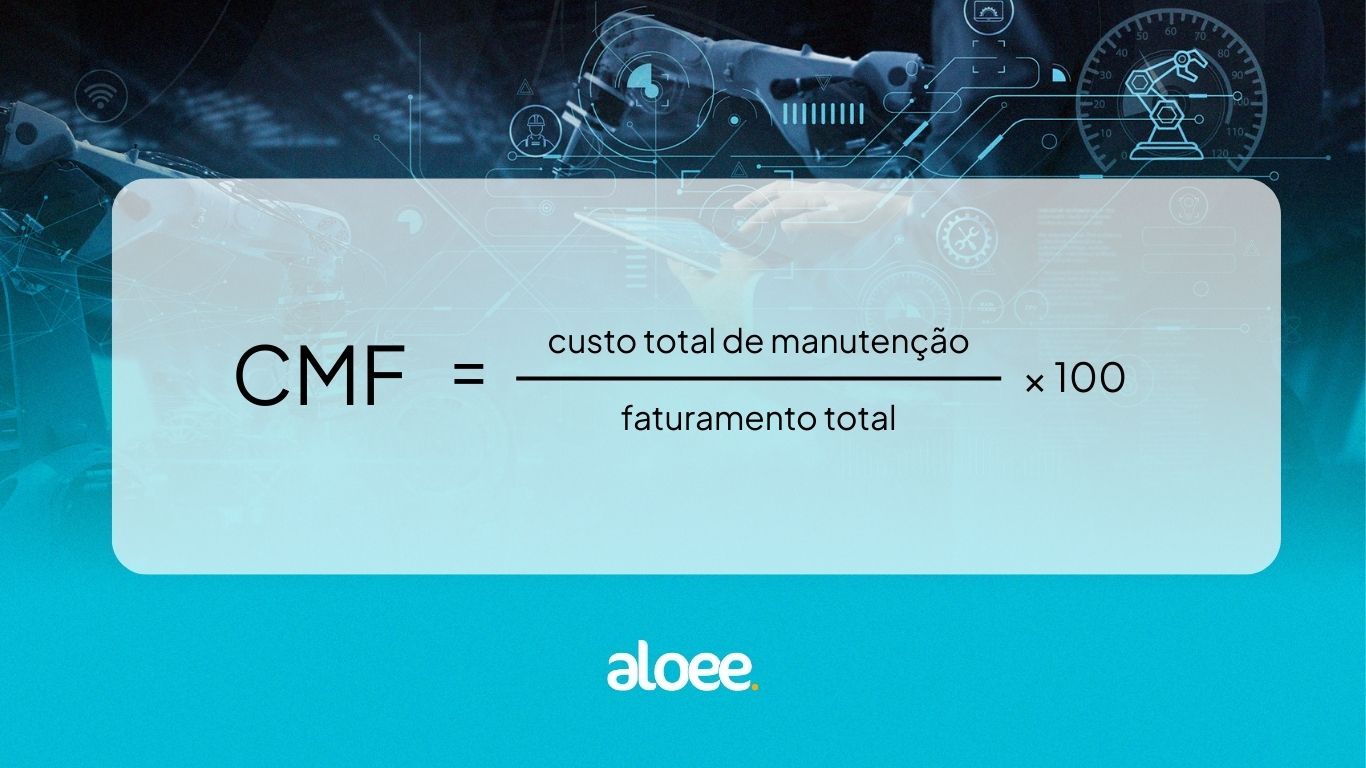
Exemplo: com um custo total de manutenção de R$ 50.000 e o faturamento da empresa de R$ 1.000.000, o CMF será de (50.000 ÷ 1.000.000) × 100 = 5%. Isso significa que 5% do faturamento da empresa foi destinado à manutenção.
7. CPMV (Custo de Manutenção sobre Valor de Reposição)
Já o CPMV compara o custo de manutenção com o valor de reposição dos ativos. Ele ajuda a determinar se esses gastos estão proporcionalmente justificados em relação ao valor dos equipamentos.
Se os desembolsos de manutenção superarem os custos de reposição, pode ser mais vantajoso substituir o ativo. Por isso, esse indicador é essencial para avaliar a relação entre os gastos de manutenção e a viabilidade econômica dos equipamentos.
Como calcular o CPMV
Obtenha o dado com este cálculo: CPMV = (Custo Total de Manutenção ÷ Valor de Reposição dos Ativos) × 100
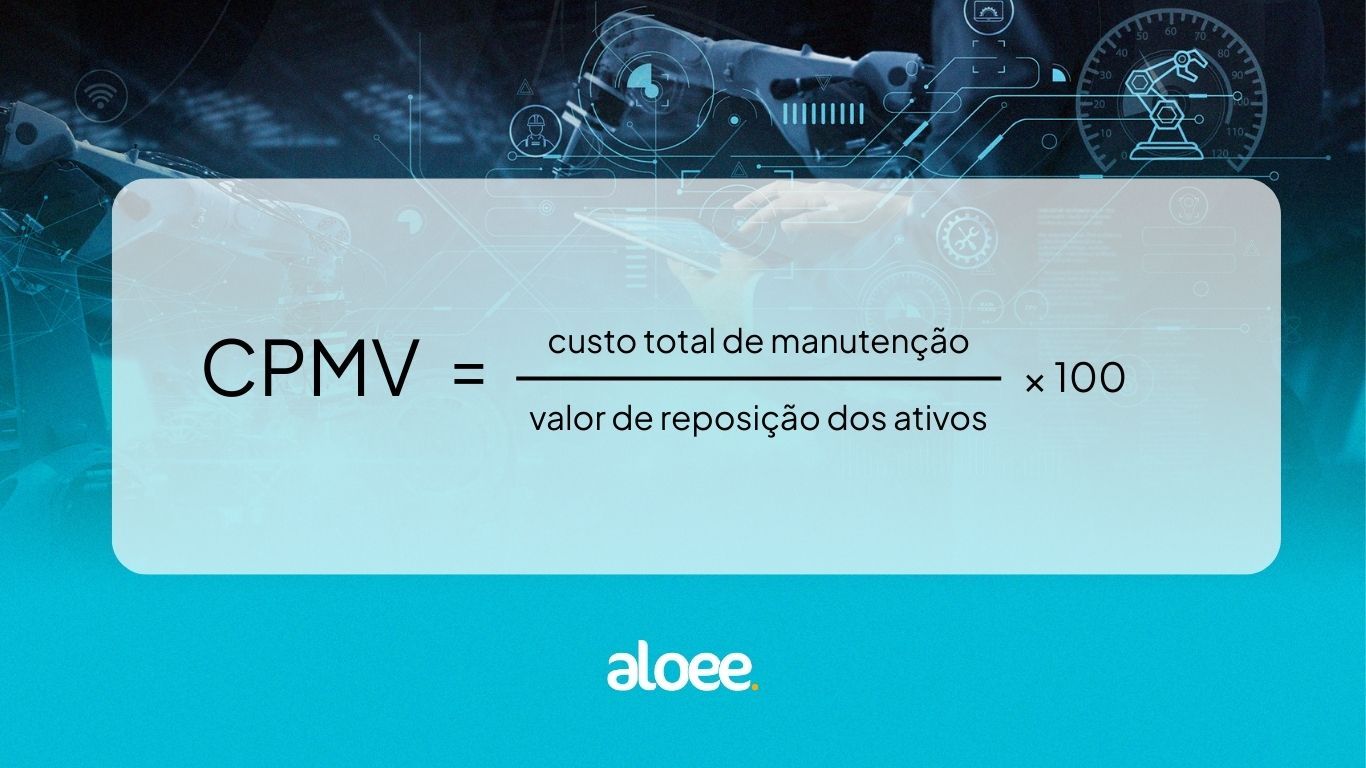
Exemplo: imagine que, em determinado período, a empresa tenha investido R$ 80.000 em manutenção e o valor de reposição dos ativos seja de R$ 2.000.000. Aplicando a fórmula, temos: CPMV = (80.000 ÷ 2.000.000) × 100 = 4%. Isto é, 4% do valor que seria necessário para repor os ativos está sendo gasto com manutenção.
8. CMUP (Custo de Manutenção sobre Unidade Produzida)
Esse indicador mede o custo de manutenção em relação à quantidade de unidades produzidas. Ele permite calcular a eficiência da manutenção em termos de produção.
Acompanhar essa métrica ajuda a verificar se os gastos de manutenção estão impactando diretamente a produtividade e a rentabilidade da empresa. Quando eles são elevados em comparação à produção, a empresa pode precisar reavaliar sua estratégia para otimizar recursos.
Como calcular o CMUP
Consiga o CMUP aplicando esta fórmula:
CMUP = Custo Total de Manutenção ÷ Total de Unidades Produzidas
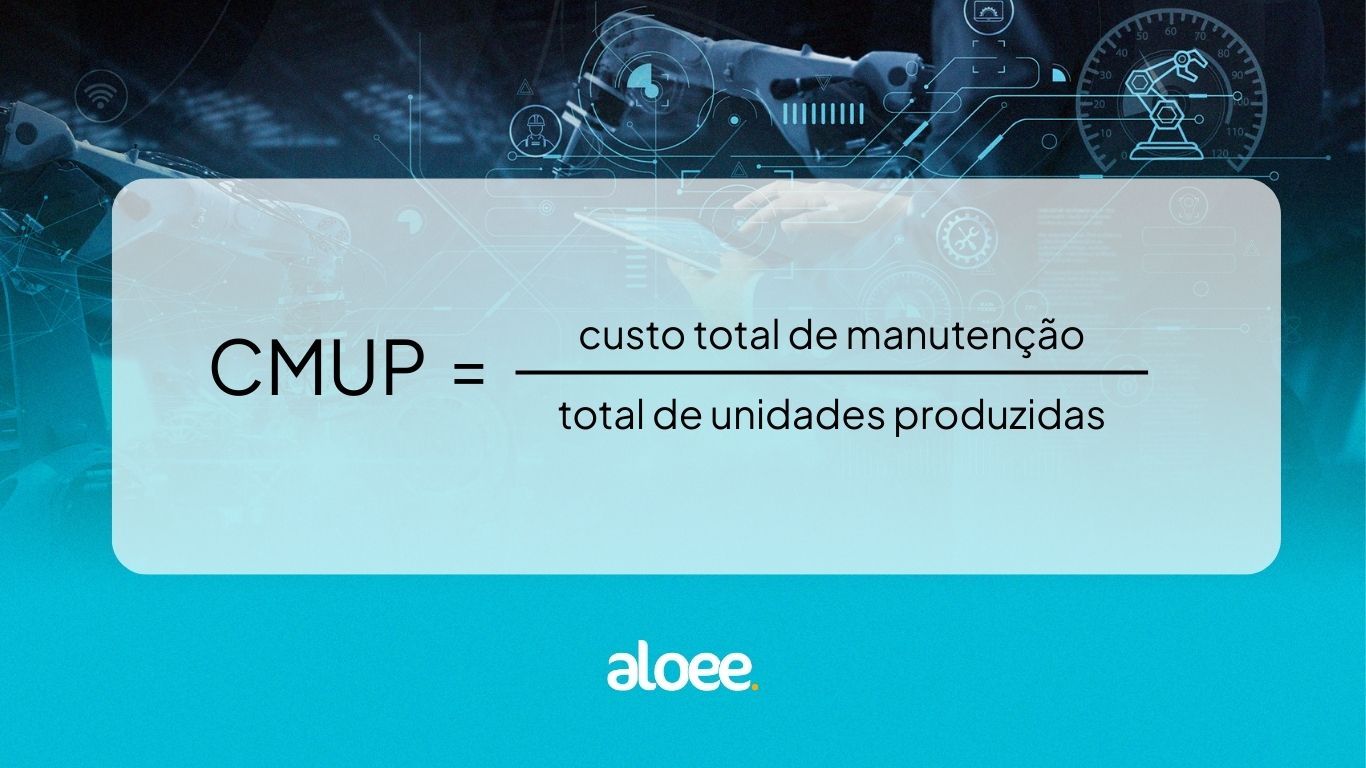
Exemplo: suponha que, em um mês, o custo total de manutenção tenha sido de R$ 50.000 e a produção total tenha alcançado 10.000 unidades. Calculando, chegamos ao seguinte CMUP = 50.000 ÷ 10.000 = R$ 5,00. Cada unidade produzida teve um custo médio de R$ 5,00 com manutenção — dado essencial para análises de margem e estratégias de redução de custo.
9. Fator de Produtividade da Mão de Obra (Wrench Time)
O Wrench Time mede o tempo efetivo que os técnicos de manutenção gastam realizando tarefas de manutenção, excluindo atividades não relacionadas à reparação, como deslocamento ou espera.
Esse indicador é importante para identificar gargalos no processo e buscar formas de otimizar a alocação de recursos. E aumentar o Wrench Time significa melhorar a produtividade da equipe de manutenção e reduzir os custos operacionais.
Como calcular o Wrench Time
A fórmula é: Wrench Time = Tempo Efetivo de Manutenção ÷ Tempo Total de Trabalho
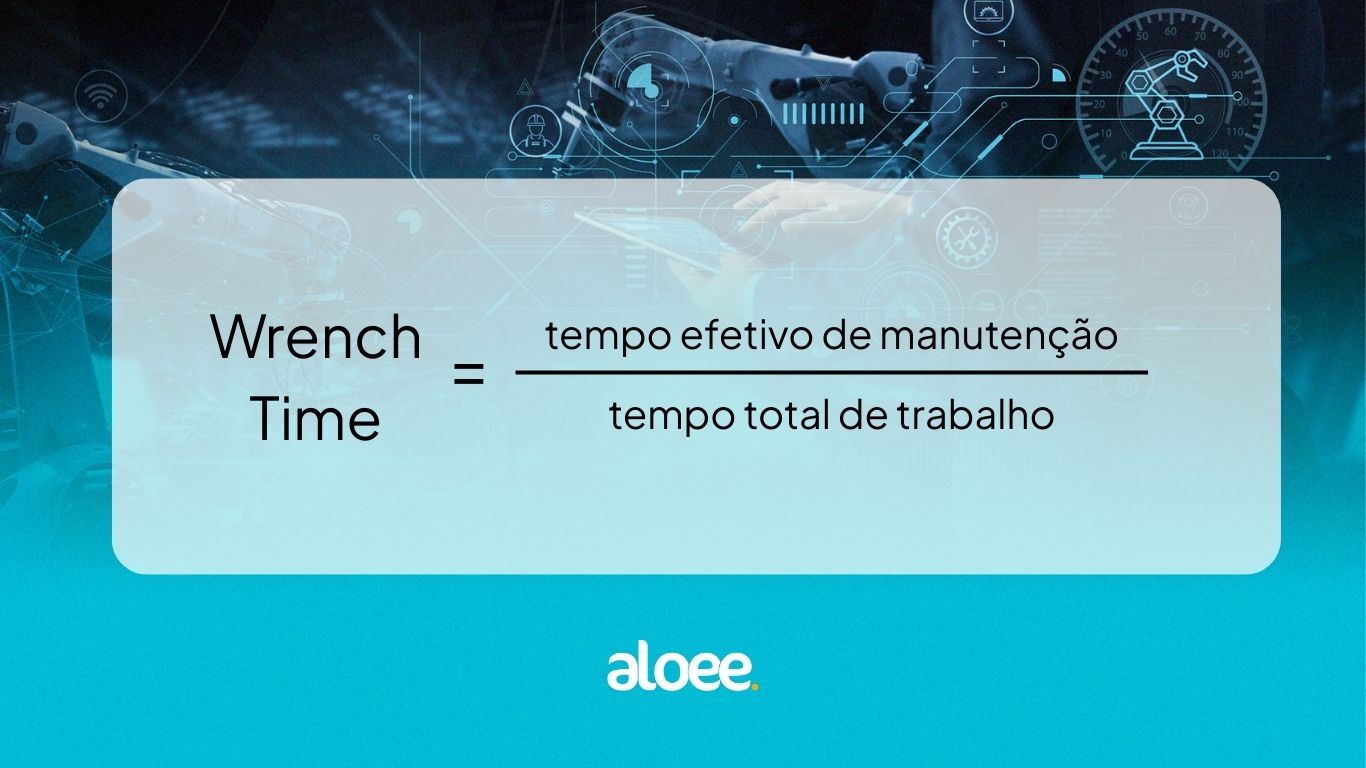
Exemplo: considere que, em um turno de 8 horas, o técnico tenha gastado 6 horas realizando manutenção efetiva e 2 horas com atividades não produtivas (deslocamento, espera, entre outras tarefas. O Fator de Produtividade da Mão de Obra é: 6 ÷ 8 = 0,75 ou 75%. Em outras palavras, 75% do tempo do técnico foi utilizado de forma efetiva na manutenção.
Tome nota! Tabela com principais indicadores de manutenção industrial
Indicador de manutenção industrial | O que é |
---|---|
MTBF | Mede o tempo médio entre falhas de um sistema ou equipamento, indicando a confiabilidade do ativo. |
MTTR | Indica o tempo médio necessário para reparar um equipamento e devolvê-lo à operação. |
Disponibilidade | Representa a porcentagem de tempo em que o equipamento está disponível para produção, em comparação com o tempo total planejado. |
Backlog | Mede a quantidade de manutenção pendente, ou seja, o número de ordens de serviço não realizadas. |
Confiabilidade | Avalia a capacidade de um ativo de funcionar sem falhas durante um período de tempo, com base no MTBF. |
CMF | Compara o custo de manutenção com o faturamento total da empresa, ajudando a entender o impacto financeiro da manutenção no orçamento. |
CPMV | Avalia se os custos de manutenção são justificados em relação ao valor de reposição dos ativos. |
CMUP | Mede o custo de manutenção por unidade produzida, ajudando a avaliar a eficiência da manutenção em termos de produção. |
Wrench Time | Mede o tempo efetivo que os técnicos de manutenção gastam realizando tarefas de manutenção, excluindo atividades não relacionadas à reparação. |
Como um sistema MES melhora a gestão da manutenção? Conte com a solução aloee
Até aqui, exploramos diversos indicadores de manutenção industrial essenciais para garantir a eficiência da produção e a confiabilidade dos ativos.
Agora, é o momento de entender como a tecnologia é capaz de potencializar esses resultados, conectando dados em tempo real à tomada de decisões rápidas e precisas. Para isso, conte com o Sistema MES (Manufacturing Execution System).
Um sistema MES oferece monitoramento em tempo real, permitindo identificar falhas rapidamente e agir de forma preventiva, minimizando paradas inesperadas. Ele também facilita a automação de processos, tornando a manutenção mais eficiente e planejada.
Além disso, ao integrar dados históricos, o MES ajuda a prever falhas antes que elas ocorram, aumentando a confiabilidade dos ativos e evitando custos extras com reparos emergenciais.
Com o MES da aloee, você tem à disposição uma solução integrada com o APS (Advanced Planning and Scheduling), acessível para pequenas e médias empresas.
Nossa plataforma proporciona uma visão clara de todos os processos produtivos e de manutenção, garantindo que você possa monitorar e otimizar sua operação de maneira eficiente e com total controle.
Experimente nossa solução! Faça um teste gratuito do MES da aloee
artigos recentes
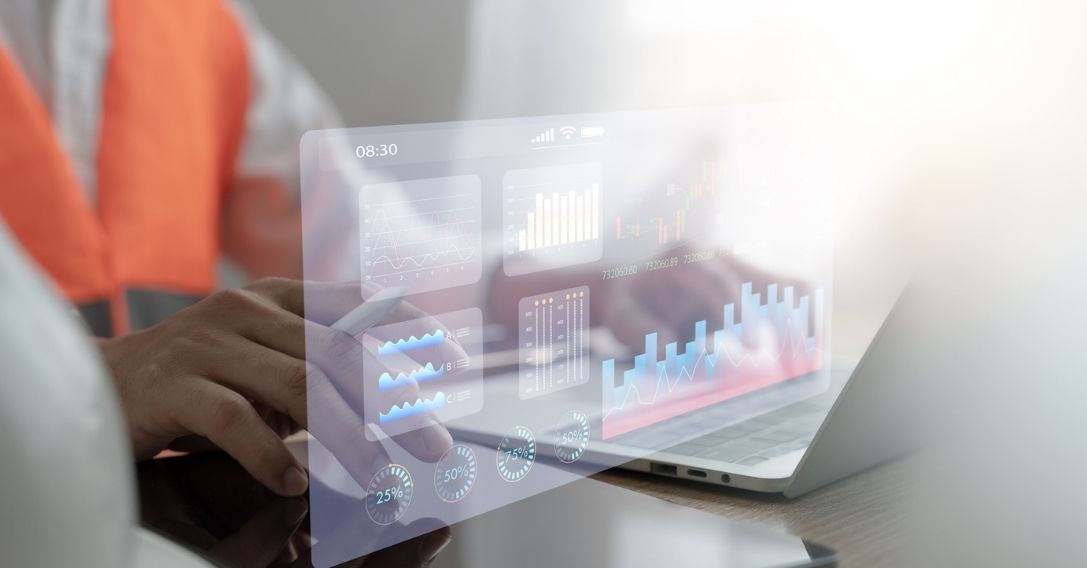